Construction process, features, and quality inspection of 3PE coated pipelines
Three-layer polyethylene (3PE) coating is a commonly used external anti-corrosion system for buried steel pipelines. This coating system combines fusion bonded epoxy (FBE), adhesive (copolymer), and polyethylene layers, delivering excellent resistance to mechanical damage and chemical corrosion.
At Haihao Group, we frequently supply 3PE-coated steel pipes for gas, oil, and water transmission projects. This article walks you through the construction process, the main advantages of this coating type, and the critical aspects of quality inspection.
Construction Process of 3PE Coating
The 3PE coating process begins with surface preparation of the steel pipe. The steel surface is cleaned via shot blasting or abrasive blasting, reaching at least Sa2.5 or Sa3 grade, which is critical for achieving strong adhesion.
Once cleaned, a fusion bonded epoxy (FBE) layer is applied by electrostatic spraying. This layer provides excellent chemical resistance and acts as the primary anti-corrosion barrier.
Next comes the adhesive layer, which binds the FBE to the top polyethylene layer. The adhesive is applied while the FBE is still tacky to ensure a chemical bond.
The final step involves extruding a polyethylene (PE) layer onto the adhesive while everything is still hot, forming a seamless and durable three-layer system. The pipe is then cooled, inspected, and prepared for delivery.
Features and Benefits of 3PE Coated Pipes
- Superior Corrosion Protection: The FBE layer effectively shields the steel surface from corrosion caused by water, oxygen, and chemicals.
- Excellent Mechanical Strength: The outer PE layer offers impact resistance and toughness during transport, storage, and installation.
- Long Service Life: A well-applied 3PE coating can extend the pipe’s service life to over 50 years under normal buried conditions.
- Wide Application: Suitable for oil, gas, and water transportation pipelines in harsh environments.
Quality Inspection of 3PE Coated Steel Pipes
At Haihao Group, we adhere to strict inspection procedures to ensure coating performance and reliability. Our quality checks typically include:
- Visual Inspection: To identify any damage, cracks, or peeling in the coating.
- Holiday Testing: A high-voltage inspection method used to detect pinholes and voids in the coating.
- Adhesion Testing: Ensures the bond between layers meets international standards such as ISO 21809 or DIN 30670.
- Coating Thickness Measurement: Using non-destructive ultrasonic methods to verify uniform coverage.
- Impact Resistance and Bending Test: Verifies the mechanical resilience of the PE layer.
Documentation such as Material Test Certificates (MTCs), inspection reports, and compliance declarations are provided with each batch.
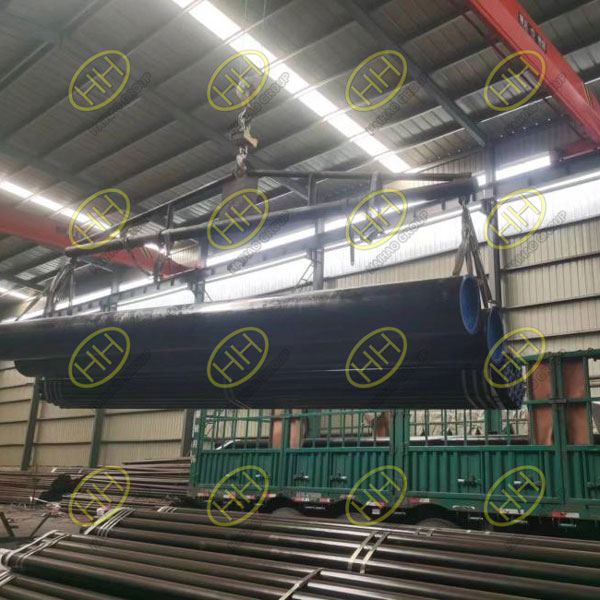
3PE-coated B36.10M pipe BE A53 Gr.B ERW SCH40 with end caps are loaded onto the vehicle and ready for shipment
FAQ: 3PE Coated Pipe
Q1: What does 3PE stand for?
A: 3PE refers to a three-layer anti-corrosion system: Fusion Bonded Epoxy (FBE), Adhesive, and Polyethylene (PE).
Q2: What are the common standards for 3PE coatings?
A: Standards include DIN 30670, ISO 21809, and SY/T0413-2002.
Q3: Can 3PE coating be used in marine environments?
A: Yes, it’s suitable for both land-based and offshore pipeline systems.
Q4: What sizes can be coated with 3PE?
A: Most pipe sizes from DN50 to DN2000 can be coated depending on line capacity.
3PE-coated pipes are essential for long-distance transmission pipelines, offering a proven balance between corrosion resistance and mechanical durability. At Haihao Group, we not only produce these coatings in-house but also perform full-scale quality inspections to guarantee reliability in real-world conditions.
If your project requires high-performance anti-corrosion piping solutions, contact our technical team for tailored support and certified 3PE coating options. Contact us for more information about our pipeline solutions. Email:sales@haihaogroup.com